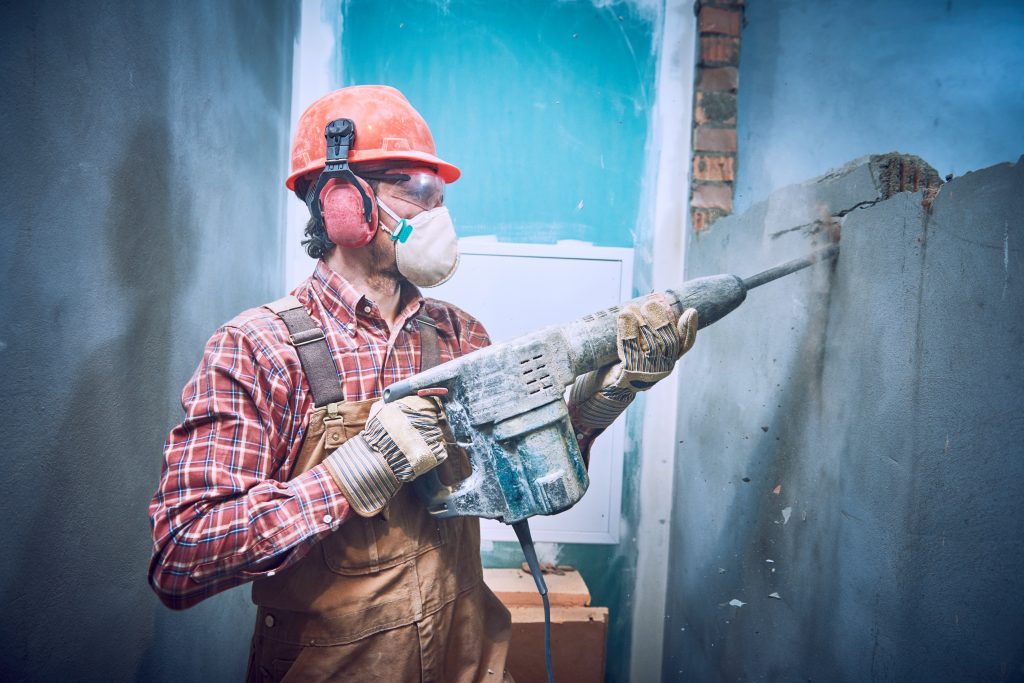
Digitized asset management – a vision of the future with added value or short-term hype?
Who last used the drill? When does the scale have to be calibrated? How many formwork panels are available on the construction site?
These are questions that craftsmen from a wide variety of industries ask themselves day after day. Answering these questions when managing operating assets takes a lot of time and energy. Both time and energy are fundamental to satisfactory work, especially in the trades. Therefore, there is no way around the correct management of resources.
Ergo, numerous providers have ventured to design programs that are intended to simplify the maintenance and handling of drills, scales, etc. What unites the providers is the promise of simple, digitally managed administration, usually linked via the Internet. But theory and practice are worlds apart. We’ve taken a closer look at the concepts of some providers and investigated the question of whether the use of equipment management software is really worthwhile.
Why digital asset management with the PC alone is not enough
The days when inventory was done with pen and paper are far from over. There are all kinds of painters, tilers, and other craftsmen’s guilds that cling to the supposed advantages of analog asset management or do not even bother with it.
Nevertheless, the proportion of businesses that manage their resources digitally is growing! Pen and paper are being used less frequently, and PCs and laptops are being used more often for resource management. But this is already where progress ends in many companies in the skilled trades, especially in the construction industry. Because numerous data are entered by employees according to different patterns. So it is not only about working with a PC. It is about much more than that!
Data entry – but correctly
A prime example of this dilemma is date entry. For example, May 9th, 2020, is often noted as 5/9/2020. However, it is not uncommon to find spellings like 4.05.2020, 4 May 2020, or Monday, 4 May 2020. This jumble makes targeted use of the data and thus the management of the operating assets is immensely difficult. However, this is of utmost importance, because if work tools or protective equipment are not checked properly, high fines may be imposed.
If an accident occurs, for example, because a lifting platform has not been maintained, the insurance company will take issue and refuse to compensate for the damage. That’s why digital equipment management is preferable to analog management – as long as it is carried out according to clear specifications.
One cloud software for everything
The demand for sophisticated and efficient management systems for operating resources has put various corporations on the map. At the time of this writing, a Google search for “digital asset management” already brings up 167,000 hits. But beware, some providers are trying to tie their customers to their products and services!
For example, some providers only support the management of their marketed product lines, i.e., their manufacturer-specific equipment and machines, or they only rely on their tags and barcodes. Both are a big hurdle for the user companies because the providers sometimes demand horrendous sums for their devices, tags, and sensors and force you to use these manufacturer-specific devices by using the software behind your back! Thus many prospective customers decide against smart enterprise management with a professional program and try to provide in their direction for order.
However, the decision to “go it alone” in terms of equipment management is filled with danger, because even in the case of conscientious management of equipment, unforeseen complications loom. For example, if the PC on which the resource management is carried out is damaged, the data records are lost. Even companies that back up their data using servers or on external hard drives are by no means safe from data loss. Accordingly, a cross-manufacturer and cross-device usage option are of great importance. Software that lists only a fraction of the devices not only fails to simplify equipment management, it usually complicates it.
Tags and barcodes under the microscope
At the heart of any equipment management software are sensors. These are placed on equipment with a special adhesive, also called tagging. The identification is done either by RFID (Radio Frequency Identification), Bluetooth, or manual scanning. Unfortunately, RFID technology has not been able to establish itself, despite promising properties, because the technology was too expensive and too unreliable.
Thanks to the rechargeable battery, for example, power-independent close-range radio sensors are possible that either transmit Bluetooth signals or are afflicted with a scan code. In this way, an ID can be assigned to each device. Customers can vary the scope of their sensor-based devices as they wish and, if necessary, change the management assistant or return to their previous system. Also promising here is so-called NFC tags, which are based on RFID technology, but is only used for near-field communication. You know these from various systems such as locker systems in swimming pools, key switches, and the like.
All these technologies are suitable for identification with a mobile device (smartphone/tablet). The near-field technologies only need to be activated: When the user goes near the device, it is displayed in an app or cloud-based platform – including location and device details.
Robust and proven: 1D, 2D barcode or QR code
Time-tested, robust, and functional is of course the printed barcode. If the code is to be scanned, the camera of the smartphone/tablet must be used. This alternative offers advantages and disadvantages. On the one hand, the battery of the mobile device is conserved and the barcode itself is of course completely powerless and uncomplicated. On the other hand, activating the camera app or the barcode identification program takes time – as does the scanning process. Thanks to the modern 2D structure, which is used by almost all providers, the scanning process is now very fast and error-free. Another advantage of barcodes is that they can be produced at a very low cost and can even be printed by the user.
No matter which tag or barcode is used, at the end of the day, a wide range of information can be called up in the equipment management system at the touch of a button or finger. The employee can see where the device is located, and when it was last serviced, charged, cleaned, tested, certified, or simply used. In the event of improper use, for example, resulting in damage during use, the person responsible is quickly identified.
Pay attention to the use of barcodes
When selecting an equipment management system, device compatibility should be taken into account. The more freely the system can be used, the greater the number of functions and the greater the flexibility of use. A provider that does not provide devices produced in-house, or at least leaves their use open, is to be preferred. In particular, the system should support the use of barcodes, as these are the simplest and most proven methods.
Cloud software does the trick
Once the equipment is identified by tag or barcode, the next step is to enter/retrieve the information about the equipment. Here, users are at an advantage who do not have to resort to additional software to be installed but can use cloud software. In this case, the data is accessed via an Internet browser, for example, Firefox or Chrome, or an app. Accordingly, no installation of software is necessary, but only a connection to the Internet! In this way, no third-party programs can access the end device, and the user’s privacy is guaranteed. Automatic synchronization has now become standard, if the result of a test date is entered in the list, it is available to all employees for viewing.
If you don’t want to miss out on the benefits of an app, you can download it from most providers or app portals. But be careful, the app itself should be provided free of charge or included in the license price. Otherwise, the use of all devices can be a considerable side item.
But whether it’s browser access or app management, using digitally managed asset management doesn’t work from one moment to the next! Tagging devices and tools, i.e. equipping them with barcodes and the like, matching them with inspection catalogs, and importing/exporting data records require an introduction.
Thus, it should be noted that the provider offers a free initial consultation, a customer-oriented implementation, and an introduction to the handling. And, compare the prices! Often, all-inclusive prices turn out to be better value for money in the long run, since the addition of countless tariffs and special functions, such as the management of non-proprietary devices, drives up the price unpredictably.
Digital asset management – definitely added value
With digitally managed asset management, you are taking a step towards working world 2.0. However, cross-manufacturer and cross-device compatibility are of great importance. Likewise, the ability to use both an app and browser access to the cloud could play a role in your choice of provider.
Moreover, outsourcing the data to a cloud always makes sense, because it relieves the customer of any problems and effort with the software itself and its operation.
You can find out more about Craftcloud’s resource management on this website.
Related Articles
Recent posts
Categories
- Asset Management 25
- Craft 41
- Customer Relations (CRM 1
- Digitization 51
- Recruitment 1
- Uncategorized 25